ITER is one of the world’s most ambitious energy projects. It will be the first fusion facility capable of producing a net amount of energy.
In France, near Aix-en-Provence, 35 countries are involved in building the largest Tokamak ever conceived: a machine that will demonstrate that fusion can be used as a large-scale energy source.
Phimeca's role
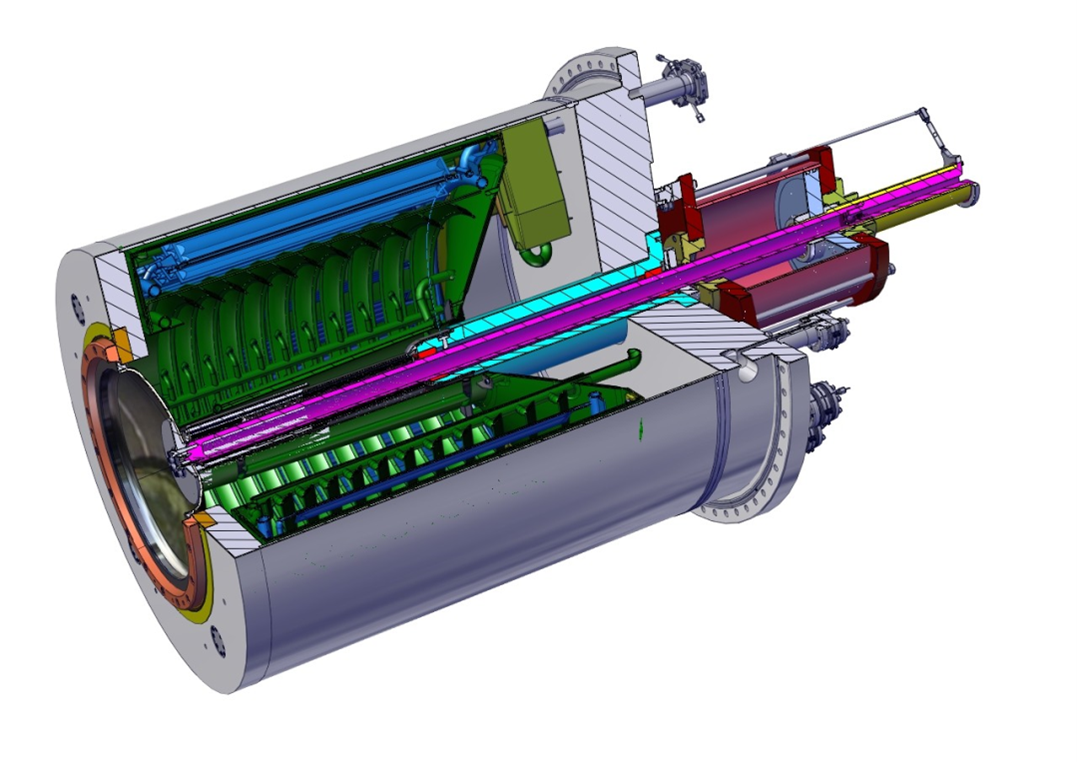
It is within this international framework that the ITER Organization has asked PHIMECA for its expertise in the field of structural calculations to validate the mechanical components of the Tokamak's Vacuum System, such as the cryopumps. These complex pumps have been specially developed to meet ITER specifications. They are based on cryogenic panels, cooled by supercritical helium circulation.
See morePHIMECA’s mission was to assist ITER at different stages of the pre-production process of these pumps:
- Firstly, upstream of the first production run, to check the pump resistance to all the loads it is likely to see throughout its life. This allowed to identify some sensitive points of the preliminary design and thus led to modify it.
- In a second phase, after a few design modifications due to the first calculation, but also to the manufacturing constraints encountered by the manufacturer, the mechanical strength of the pump as-built was verified.
These two phases are similar (except for the initial geometry provided by the customer) and both led to the delivery of a complete study report in English and an ANSYS FE (finite element) model archive.
During these two calculation phases, Phimeca performed, on a turnkey basis, the mechanical calculations of the cryopump by means of FE model simulation using the ANSYS Workbench software:
- Creation of the FE model from the geometry provided by the customer using ANSYS Design Modeler. The geometry was thus simplified, in particular with the help of shell elements.
- Definition of materials and their thermo-mechanical properties (thermal expansion coefficients and thermal conductivity).
- Definition of mechanical loads from the Component Load Specification:
- Own weight
- Operational pressures
- Earthquakes (definition of spectral response)
- Hydrostatic pressure (accidental case, pump filled with water)
- Ice accumulation on cryogenic circuits (accidental case).
- Definition of thermal loads. Conduction, convection and radiation phenomena are modeled in ANSYS. A temperature profile in operation is given below.
- Realization of a modal analysis to know the dynamic behavior of the component and to implement the spectral method on ANSYS.
- Combination of the different simple loads to model all the load cases necessary for the validation of the component..
- Stress post-treatment according to the criteria of the European standard EN13445 – Unfired pressure vessels, Part 3: Design:
- Criterion on primary stresses (membrane and membrane plus bending);
- Criterion on principal stresses in case of triaxial stress state;
- Fatigue criteria on primary and secondary stresses.
- Conclusions and writing of a calculation note.
Following the calculations made by Phimeca, the design of the cryopump was validated according to the EN13445 standard. The component could thus enter in test phase without fear of a particular failure during the tests.